1965-70 Mustang Front
Suspension Installation Instructions
Thank
you for choosing TCI’s Mustang front suspension package. The kit
has been designed to not only allow your Mustang to handle
corners, steer and brake better and have more engine compartment
room but have that low sports car stance. Although the install
will require cutting, grinding, drilling, welding and quite a
few hours of your labor, the results are well worth the effort.
I will take you through the install step by step.
Before we
get started lets show you some before and after pictures. |
 |
|
Before from the rear. |
After from the rear. |
 |
 |
Before from the front. |
After from the front. |
 |
Remove all
the old suspension components including the steering column. |

|
I used
a die grinder with a cut off wheel to cut the coils in a couple
of places for much easier removal. |
|
|
Next the shock towers, suspension
brackets, have to be removed, but first clean as much of the
underbody coating in the wheel well around the shock towers as
possible to facilitate cutting. |
When it came to cutting off all
the old suspension mounting brackets, I’ve tried a saber saw, a
die grinder with a cutoff wheel, oxy/acetylene torch and a
plasma cutter. By far the plasma cutter was the easiest,
cleanest and most accurate. |
|
|
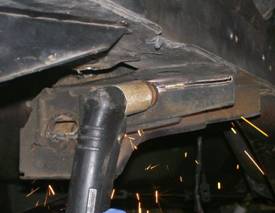
|
Start with
the lower A-arm/motor mount brackets first.
When cutting,
be careful not to cut into the main frame rail.
We will be
grinding off the material welded to the main rail. |
|
|

|
Next are the
shock towers. The first cut will be made from inside the wheel
well just above the main frame rail flange. |
 |
The rest of
the cutting will be from inside the engine compartment.
Cut the lower
edges of the tower from the frame rail. |
|
|
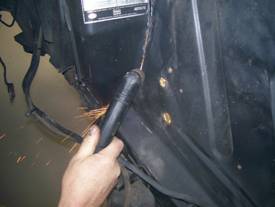 |
The vertical
cuts on the towers are made at the bend radius between the tower
and fender panel. |
|
|
 |
The final cut
is made across the top in the bend radius. |
|
|
 |
The shock
tower completely removed. |
 |
If a TCI sway
bar package is being installed go ahead and cut off the stock
sway bar brackets and the strut rod support channels.
This is
highly recommended for superior handling and cleaner appearance. |
|
|
 |
Remove all
excess material, welds and paint from the main rails to all for
the installation of the boxing plates.
Remove excess
material around shock tower opening until it is flat to the
fender panel; also straighten up inside cut lines for clean
appearance. |
|
|
 |
The outer
flange on the top of the main rail has to be removed.
Draw a line
through the centers of the spot welds.
|
|
|
 |
Carefully cut
the flange off, leave about 1/8” or so extra material.
Use a grinder
to remove the last 1/8” material.
If you try to
plasma cut the entire flange off in one pass you will remove too
much material from the frame rail. |
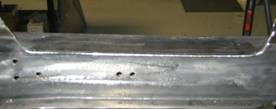 |
All the
grinding is done.
Although you
cannot see it in the picture, there is a split between the top
and the side rail metal. |
|
|
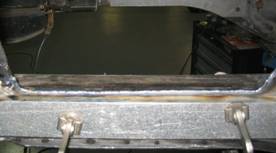 |
The top and
outside of the rail will be seam welded back together.
Clamp a two
foot flat piece of material (I used 1” x 2” aluminum bar) about
3/4” down from the top of the frame rail to maintain a straight
edge.
|
Massage down
any high spots or irregularities that aren’t straight and square
with a small hammer.
Finally, weld
the seam and side together also include the short flanges going
up. |
 |
Next grind
the welded area flat and square.
At this
point, you are done removing parts and preparing the frame
rails.
This is a
good point to do any other engine compartment cleaning you would
like. |
|
|
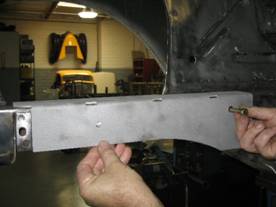 |
You are now
ready to start installing the boxing plates to strengthen the
frame in the cross member area.
The folded
inside boxing plates are located by using a bolt and aligning
the rear holes in the folded bracket with the upper front
steering box hole (drivers side 7/16” x 3” bolt) and the upper
idler arm hole (passenger side 3/8” x 3” bolt).
|
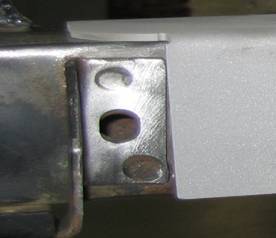 |
If the stock
sway bar bracket was not removed, you will have to notch the
inside flange one inch back for the locating holes to line up.
Check to make
sure boxing plate sets totally flat all the way around on the
stock frame rail. |
|
|
 |
Install the
correct outside boxing plate with the bolt and fasten with nut.
(The plate with the hole closest to the rear is the passenger
side.)
Align the
boxing plate edge parallel with the top plate exposing an
even section of the stock frame that when welded will tie
both boxing plates to each other and to the frame. |
|
|
 |
This is a
close up of the parallel edges referenced above with a weld tack
for reference. |
|
|
 |
It is
critical that the two edges are parallel even if you
have to trim off of the bottom edge of the outside boxing plate.
This is
because the 3/8 inch holes when drilled straight through after
welding serve as a location origin for the cross member locating
plate and the A-arm/shock tower (shown on left). |
 |
After
clamping boxing plates using support plates double check to make
sure plates are flat on the frame rail and as close to 90
degrees as possible to each other. |
|
|
 |
It’s time to
tack weld inner and outer boxing plates to each other and to the
frame. When it comes to welding, I prefer to heli-arc because
it’s cleaner and less grinding afterwards but a wire feed will
work fine, just a little more clean-up grinding afterwards. |
|
|
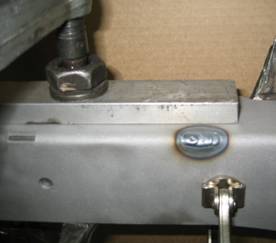 |
The rosette
welded three slots in the folded boxing plate tie it to the
frame.
Note; the
rosette weld to the left is not done yet. |
|
|
 |
Weld the
outside boxing plate totally 360 degrees around tying it to the
frame and the inside boxing plate. |
 |
Weld the
inside boxing plate on the top, ends, sides and rosettes.
The portion
following the bottom line of the frame will be welded later.
|
|
|
 |
Install the
formed bottom boxing plate using a 1/2”-13 x 1” bolt into the
stock lower tube support bolt hole.
Install with
the straight edge facing in and the curved and notched edge
facing out.
|
|
|
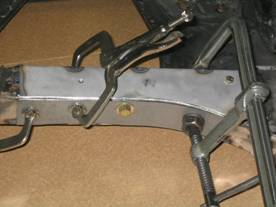 |
Align inside
edge of the bottom boxing plate even with the edge of the inside
boxing plate.
Clamp
securely checking for flatness. |
Tack-weld
lower boxing plate. Weld inside edge to frame and inside boxing
plate tying both together. Weld boxing plate on the underside of
the frame. Don’t weld the out side edge at this time.
|
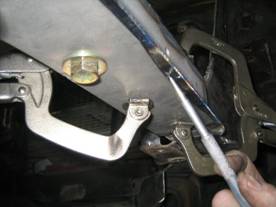
|
The outside
edge of the frame is where the two stamped flanges of the frame
are spot welded together and will require clearance grinding for
the coil-over before welding.
|
|
|
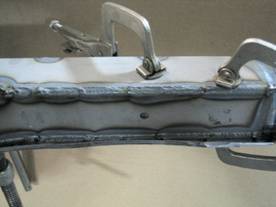 |
The entire
length of the stamped flange edges needs to be removed.
Using the
outer edge of the lower boxing plate as the template, grind the
two flanges till they match the profile of the boxing plate
edge. |
Turn the heat
up on your welder and seam weld both frame flanges and the
boxing plate edge together. Remove the ½ inch bolt and weld up
hole.
|
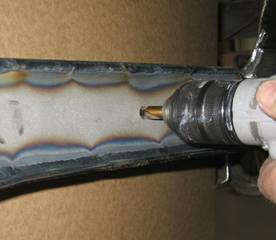 |
Drill the
frame through from both sides in the 3/8” hole in the boxing
plates to make the locating point.
Time to make
it all look good.
Grind and
sand the weld edges, round the corners and weld spot fill any
pits or imperfections for a clean finish. |
|
|

|
You are now
ready to start installing the cross member and shock towers.
First install
the one inch wide locating plate using a 3/8 inch bolt and nut
through the 3/8 inch hole drilled in the boxing plates a few
steps ago. |
|
|

|
Next slide
the cross member (steering rack brackets forward) between the
rails behind (firewall side) the locating plates.
You may have
to trim the ends slightly to get the cross member to tap in.
Trim equally from both sides.
You want a
tight fit so tap the cross member in with a soft mallet.
Use a sturdy
flat cross bar (approximately 32” long), two short flat spacers
(two inch’s) and a long c-clamp to pull the cross member up
tight against the bottom of the frame and snug up against the
locating plates. |
|
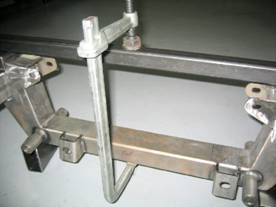
|
|
|
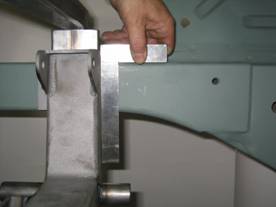
|
Next check to
make sure that the cross member is 90 degrees to the top of the
frame. This is critical for correct engine angle and lower A-arm
angle.
Corrections
can be made by slightly trimming the front or rear edge of the
cross member that contacts the bottom of the frame. |
 |
Double check
for square and tack weld all sides and on the bottom.
Remove the
locating plate and finishing welding all the way around,
switching from side to side so as to not build up to much heat.
Don’t weld up the inside 3/8 inch hole yet as it will be used to
locate shock towers. |
|
|
 |
The
a-arm/shock tower bracket is mounted with the highest a-arm bolt
slot forward and the lowest slot rearward.
This is the
built in anti-dive feature.
Using a 3/8
inch bolt fasten the tower to the frame rail checking to make
sure bracket sets flat against the boxing plate. |
|
|

|
Use a C-clamp
from the inside and pull the bracket down snug to the top of the
frame rail.
When
everything is tight, tack weld all the way around then finish
weld. Next, remove the tab with the bolt hole in the shock
clearance relief and finish weld. Weld up the four 3/8 inch
locating holes and finish grind for a clean appearance. |
 |
The sway bar
bracket is mounted 12 inch’s from the front edge of the cross
member to the center of the bracket.
Clamp
securely to the bottom of the frame with the wings flush against
the inside of the frame and weld. |
 |
Completely
welded. |
|
|

|
The lower
a-arms are installed with the sway bar bung facing forward. The
5/8 inch shaft is installed with the acorn nut facing forward
with a thin stainless washer on both sides of the urethane
bushings on the a-arm. |
|
|
 |
Install the
a-arm onto the cross member and install the nylock nut using
anti-seize on the threads and tighten. |
|
|
 |
The shock
assembly is installed next using the ½ inch bolts. |
 |
When using
Shock Waves with a spherical bearing, a provided spacer will be
required on each side of the spherical bearing. |
|
|
 |
Install the
upper a-arm (both the same) with the shaft on the inside
of
the tower.
Install the button head 9/16 bolts from the outside through the
tower then the camber adjustment washers then through the a-arm
and install the nylock nut with anti-seize on the threads and
position the a-arm bolts in the center of the caster slots for a
starting point and tighten the nut. Note: Start with 4 thick
washers per bolt-drivers side and 2 thick washers per bolt
passenger side, the driver’s side frame rail is wider than the
passenger side. |
|
|
|
|
 |
The spindle
and brake assembly comes completely assembled with the bearing’s
packed and seals installed and is installed next. With the
steering arm forward and caliper rearward set the spindle onto
the lower ball joint and install AN washer and nut, tighten and
cotter pin. |
|
|
 |
Install the
top a-arm ball joint into the spindle. Install AN washer and
nut.
Tighten and
cotter pin. |
|
|

|
The rack
assembly needs to be centered to allow equal steering left to
right. On a bench, turn the pinion out to lock one way.
Measure from a convenient point to the end of the tie rod. (This
rack was 17 ¾). Turn the pinion to the opposite lock position
and measure from the same point to the end of the same tie rod
(11 ¾). 17 ¾ minus 11 ¾ = 6. Divide by 2=3 Add that number to
the smallest measurement (11 ¾” + 3” = 14 ¾”) and turn the
pinion back till you get that measurement and your rack is
centered. |
|
|

|
Install the
rack using the two 5/8” bolts, washers and nylock nuts with
anti-seize on the threads and tighten. |
 |
Clamp a
straight edge to each rotor as shown then using a tape measure
front and rear; set the toe-in approximately 1/8” for a
starting point. |
|
|
 |
Install the
tie rod end jam nut and then the tie rod end turning it an equal
amount of turns per side until they line up with the steering
arm tapered hole. Check the toe-in again, adjust if needed. |
|
|
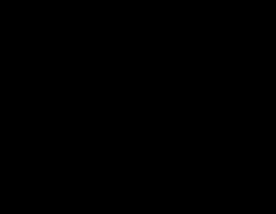 |
Install the
sway bar (center drop of bar down) next using the four 3/8”
bolts, washers and nylock nuts. The spacer plate goes against
the frame bracket first then the saddle bracket next. |
|
|
 |
Before
tightening, center bar equally both sides. |
|
|
 |
Install the
½” rod ends as shown with the male end facing up. The sway bar
rod end link needs to be straight up and down to allow adequate
rack and pinion tie rod lock to lock clearance. Adjust by
sliding the sway bar for and aft then tighten bracket bolts. |
|
|
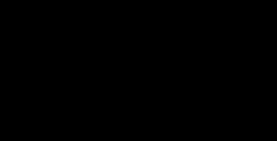 |
I chose an
Ididit brushed steel two inch diameter tilt retro fit steering
column (TCI # 326-3100-00) and a Borgenson steering linkage
package (TCI # 310-3120-03) to connect the rack and pinion to
the steering wheel. |
|
|
 |
The stock
dash mount bracket was used with the 2 piece steel reducer that
Ididit furnished. Note: The reducers kept sliding out as I was
installing them so I tack welded the top shell to the top
bracket and drilled an 1/8 inch hole in the bottom shell and
bracket and pop-riveted the two together. |
|
|
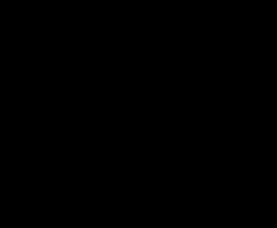 |
I chose to
fabricate a lower column mount that would fit the existing hole
pattern and support the bottom of the column with two set screws
on the inside for a simple clean look.
TCI part #
000000000 |
|
|
 |
With the
column installed, put the Borgenson universal joints onto the
end of the column and the pinion on the rack. The power rack and
the column were both ¾”-36 spline X ¾” DD. |
|
|
 |
Correctly
measure as shown and cut shaft to length. When in doubt cut a
little longer and trim to fit. Shaft must never extend past
flush with the inside of the yoke this will cause an
interference problem and system failure. |
|
|
 |
The rack will
have to be unbolted and slid forward to install the shaft. |
|
|
 |
Loctite the
set screws before tightening and loctite the jam nuts. |
|
|
 |
To install
the inner fender panels loosen the center fender bolts and
remove the one over the shock tower. Position the correct panel
over the a-arm and slide lip under the fender till the bolt
holes line up on top and the three on each side of the panel
with the existing stock inner panel holes. |
|
|
 |
Install the
5/16 button head bolts in the existing holes and drill the lower
two holes in each side of the panel. |
|
|
|
Install
remaining bolts, tighten and finish by tightening the stock
fender bolts. |
|
|
 |
A 235-40 tire
on an 18” rim was chose for adequate fender clearance. Correct
ride height is with the lower a-arm level to the ground. Adjust
the height with the threaded ring on the bottom of the
coil-over.
Castor 4-5
degrees positive with Power steering.
Camber 0
degrees. Toe-in 1/8”. |
|
|
 |
The spring on
the coil-over is 350 lb. If you are using aluminum adjustable
shocks adjust the damping knob all the way counter-clockwise
(soft) and turn clockwise 3 clicks for a starting point.
You are now
ready to install the power train assemble. |
|
|